Private Networks for Manufacturing
Best practices in designing indoor and outdoor private networks.
by Dean Bubley of Disruptive Analysis | A thought-leadership eBook.
Summary
The manufacturing sector is one of the most promising industries for emerging private LTE and 5G networks, as well as adjacent technologies such as edge computing and new Wi‑Fi 6E/7 versions.
Companies in this field are deploying many applications with extremely demanding requirements for wireless connectivity in terms of bandwidth, predictable latency, security and uptime. Given well-defined sites and a growing supplier ecosystem, manufacturers are rapidly becoming a key target for private wireless vendors and solution integrators.
Some sub-sectors, such as large and highly automated factories producing vehicles or electronics seem to be most advanced. Continual-process plants such as cement and steel production have less adoption so far, but significant medium-term potential. Smaller-scale or artisanal manufacturing will likely lag.
Unlike many industries, some manufacturing firms have long had sophisticated network infrastructure, often integrated with IoT and automation systems (“OT”, or “Operational Technology”), as well as more conventional IT and telecoms needs. Historically, there has been wide use of specialist technologies such as Industrial Ethernet, as well as variety of niche and proprietary wireless systems.
That said, other manufacturers are still quite “analogue”, with manual processes and unconnected systems. These are becoming “transformed”, although progress still varies widely by country and sector.
Key strategic focus areas include improved productivity, performance, flexibility and quality – all of which require better data, decision-making and “closed-loop” automated actions, often in real-time.
In essence, what is happening is a form of convergence:
Together, this is creating a perfect match of supply and demand for private mobile networks, for OT and general IoT and operational needs. This paper outlines the main use-cases, deployment scenarios and paths to private 4G and 5G in factories and similar industrial plants.
While this report has focused on the radio aspects of private 4G/5G, it is important to recognize that the broader ecosystem – from core networks to edge computing and planning / design / test systems – is evolving in tandem, along with a huge ecosystem of systems integrators and vertical specialists. In manufacturing organizations like the 5G-ACIA (Alliance for Connected Industries and Automation) are defining best practices and standardized terminology.
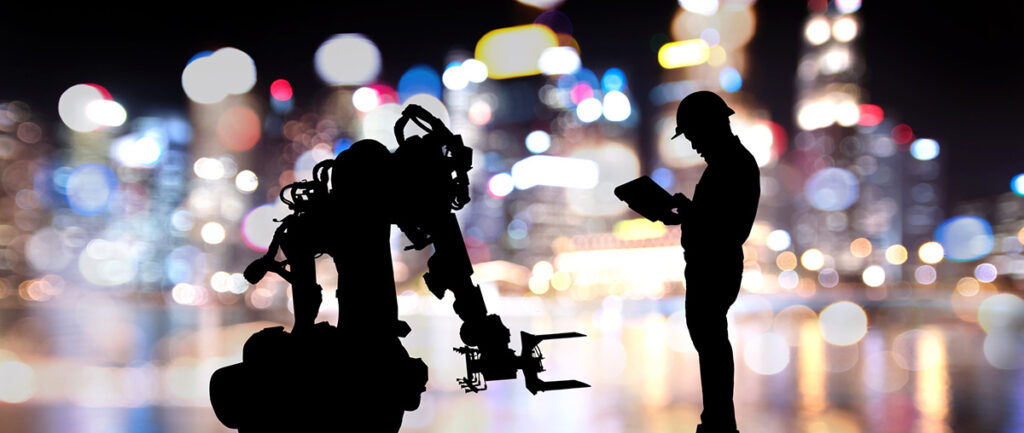
Definition of the manufacturing sector
There are numerous manufacturing sub-sectors and site types covered in this report. Although there are many common features and market drivers – notably their inclusion as part of Industry 4.0 vision – there are also clear differences in locations’ physical size and layout, as well as machinery and application platforms, regulatory oversight and technology conservatism.
The key domains covered in this eBook include:
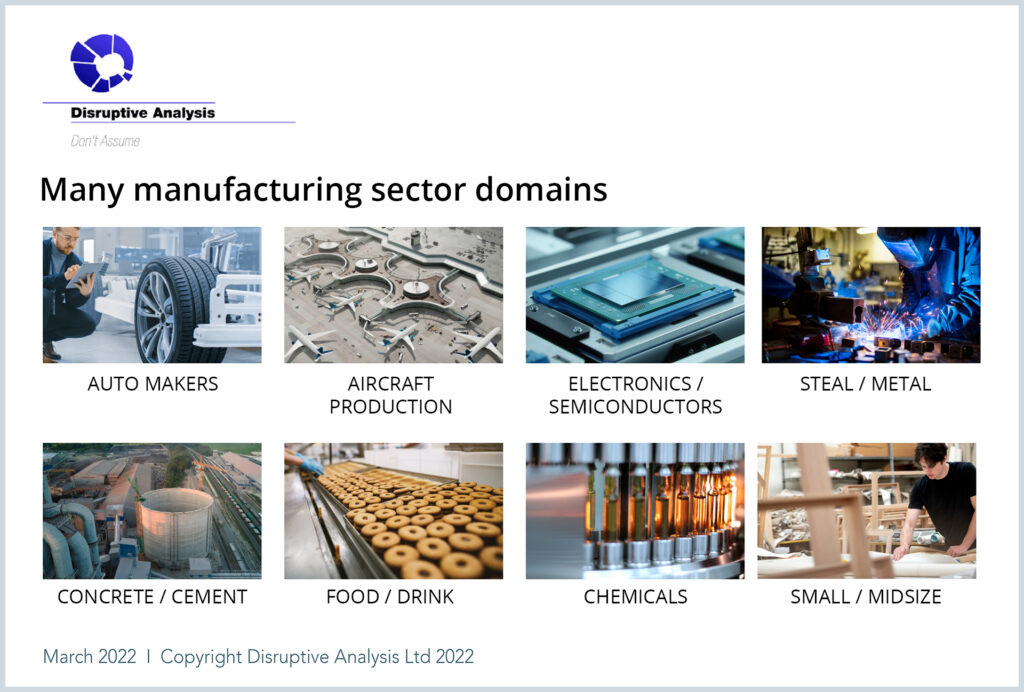
Logistics, transportation and warehousing are all hugely important in the manufacturing supply-chain but will be covered in a separate eBook.
Broadly speaking, process industries tend to require large plants, often in continuous operation, and perhaps with dangerous materials such as flammable liquids and pressurized gases. Discrete manufacturing takes place at a wider range of scales – from small individual artisans, up to the largest automotive factories or semiconductor fabrication sites.
It is important to note that large factories and manufacturing plants have numerous types of machines and equipment to connect, from welding machines to industrial ovens, and from indoor cranes to mobile robots and conveyor-belt systems. Some move, some are static. Some are old (legacy) equipment with non-standard interfaces and minimal onboard compute/data capabilities, while others are brand-new units designed with AI and cloud/edge control in mind. In many cases, the “machines” may have multiple internal networked elements such as cameras, sensors and controllers, as well as connecting externally to other machines, or external IT systems.
In other words, manufacturing is highly heterogeneous. While a new factory for building electric vehicles (EVs) or a recent semiconductor fab could be a “greenfield” project started from the ground up, that is the exception rather than the rule. Many networking projects will take place in existing buildings, perhaps adding a new machine or process, or retrofitting sensors and analytics to existing machinery.
Key challenges and market drivers
The demand for private networks for the manufacturing sector is ultimately driven by a number of top-level national and global changes. Broadly speaking, these all create a greater requirement for connectivity, control and information flows – which then translates to more 4G and 5G networks, as well as Wi‑Fi, fiber and wide-area network services.
Note: “Industry 4.0” tends to be used as a popular umbrella term for a variety of connected, information-driven transformations of manufacturing and other industrial sectors. Also sometimes called “digitalisation”, it refers to a broad move towards automation, the linking of IT and OT (“Operational Technology”) domains and the increasing role of connected devices and sensors (IoT, Internet of Things).
Some of the key “megatrends” for manufacturing include:
Combined, all of these broad factors, as well as company- or country-specific trends, are combining to mean that networks need to be:
There is also a need for new network systems (such as 5G or Wi‑Fi 6/6E) to integrate with legacy connectivity types. This spans many different types of networking, both wired and wireless.
Many names of cabling types and communications protocols will be unfamiliar to those used to standard Wi‑Fi or ordinary fiber deployments – for instance ModBus and Profinet networks for industrial systems, or MQTT and OPC UA messaging protocols. IP-based networks are far from ubiquitous. In addition, there are numerous considerations and regulations about electrical shielding, safety and so on – consider for example possible RF interference from welding machines or metal particles in the air.
This means that the adoption of new wireless technologies such as 5G and Wi‑Fi 6E will take time – especially as these technologies are themselves still evolving. Many of the more “Industry 4.0” features of 5G only become available in future, with later 3GPP Releases 16 / 17 / 18. This means that often multiple technologies will be used in combination, with a variety of integration or gateway approaches needed.
(Also, outside the scope of this document, there is a huge amount of additional change occurring with network management and control, including cloud- and edge-based core networks and operational systems).
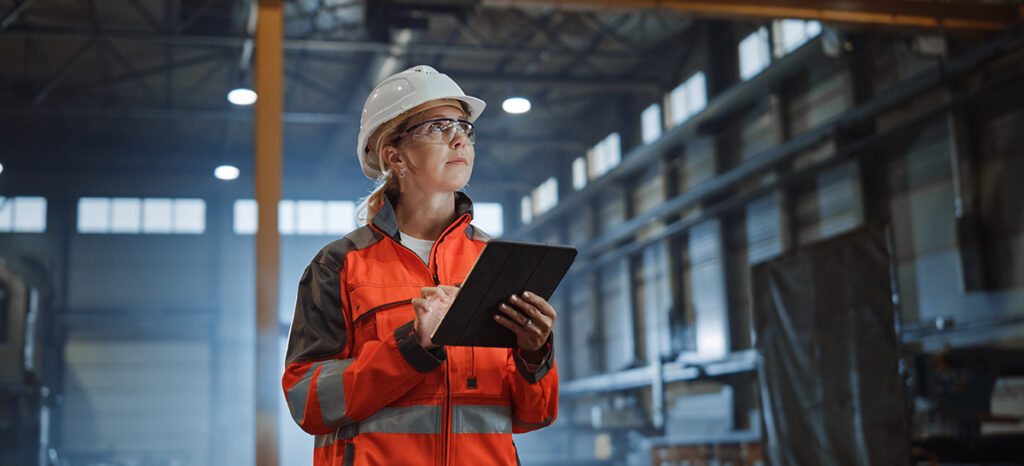
4G/5G use-cases in manufacturing
Given the industry structure and changes outlined above, there are two layers of questions to address in this report:
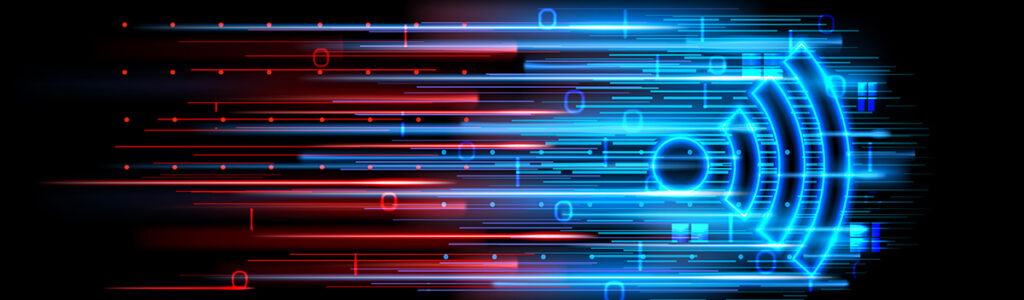
This section highlights some of the emerging use-cases that can benefit from cellular connectivity in the manufacturing sector, especially auto-makers, electronic and chemicals producers, which are probably the largest customers for private 4G/5G at the moment.
While there are likely hundreds of applications overall – and some such as general office IT are omitted for conciseness – the following are typical of the aspirations of many companies in these sectors.
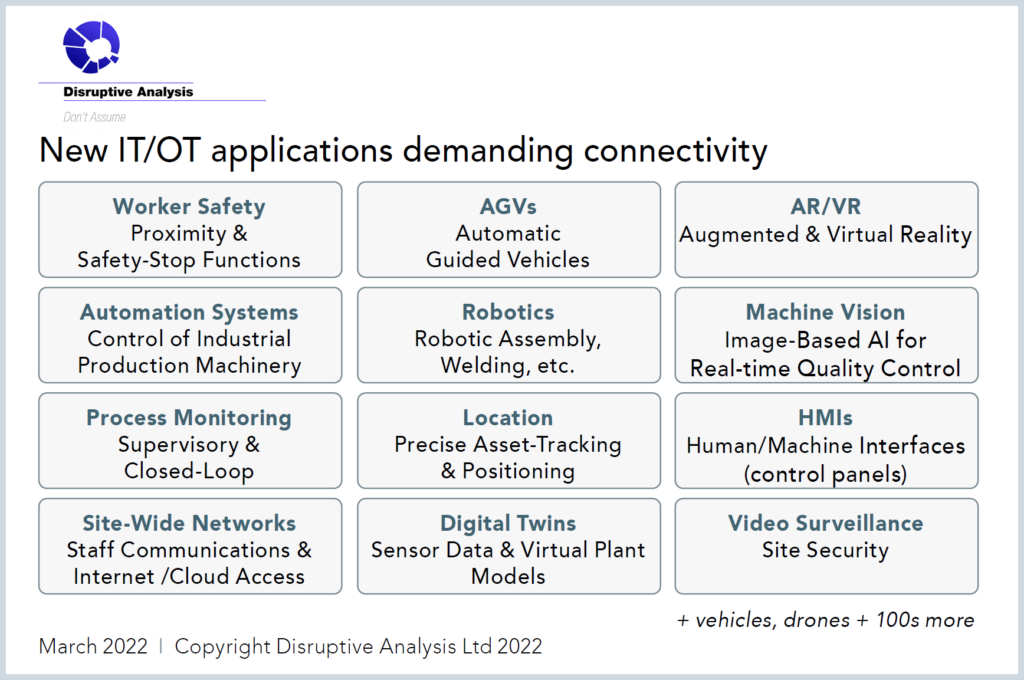
Worker safety systems
A key application for private networks in factories or other industrial settings is enabling companies to maintain worker safety more effectively. There are a number of elements here requiring good connectivity:
Depending on the specific site, these functions may be needed both inside buildings and outside, and even in underground areas or inside large items of equipment such as storage tanks.
Private 4G/5G allows for reliable connectivity, with customized coverage and uptime guarantee that would be hard to obtain from public networks.
Automated guided vehicles (AGVs)
In many industrial settings, mobile robots are used to move material, equipment or components, either inside one factory or warehouse building or between them. Such automated guided vehicles or AGVs usually follow specific pathways and move quite slowly for safety reasons, separated from human workers. Increasingly however, they can use connected cameras or sensors to analyze their surroundings, for safe use of the same spaces as human operators.
5G-based guidance and control can enable AGVs to move safely and rapidly around the plant, as well as interact accurately with other machines such as conveyor belts, lifting systems or electrical charging points. URLLC (Ultra Reliable Low Latency) capability and onboard cameras allow edge-cloud integration and oversight – or remote driving.
AR / VR processes and training
Manufacturing sites are already proving to be early adopters of augmented and virtual reality technology – a field that is also starting to be renamed as “metaverse technology”. AR headsets and other devices enable operators to work hands-free on complex tasks, while seeing assembly or maintenance instructions and data displayed into their fields of view. Although Wi‑Fi tends to predominate for these use-cases, 4G/5G is becoming important for outdoor scenarios, or in sites with network congestion and interference.
Designers can use VR to visualize new product concepts, or to allow them to “walk through” a virtual factory to view and configure potential new process and machinery layouts. Simulations can identify the behavior of human workers in new industrial processes, or help designers understand ergonomics of new products, before building physical prototypes. A wide variety of training tasks can benefit from AR/VR techniques.
4G/5G connectivity – as well as Wi‑Fi 6/6E – can enable also real-time AR streaming with some graphics tasks offloaded to edge-computing resource. This reduces the processing power required on the headset or tablet itself, extending battery-life or reducing the weight needed. While few headsets are directly 5G-capable today, they can be tethered to a wireless modem or Wi‑Fi access point.
Automation Systems
The core of many manufacturing facilities – especially for automotive and high-tech production – is automation. There are multiple layers of compute and communications here, from control of individual machines using PLCs (programmable logic controllers), through to broad, multi-step processes involved along a production line.
All of this requires connectivity. In particular, specific machines or processes often have extremely high reliability requirements, as well as low (and deterministic) latency needs. While fiber connections and various proprietary solutions have been widely used in the past, 5G offers the potential for greater flexibility and/or lower costs in future. It should be stressed, however, that “5G-only” factories are highly unlikely. Most automation systems suppliers work with multiple network types, integrating the most appropriate for each machine and application.
That said, there will be strict testing and deployment planning needs to ensure reliability, given the costs of “downtime”. This is likely to mean the more advanced manufacturing companies lean towards private, dedicated networks for automation.
In addition, advanced manufacturing plants are continuing to evolve. They are looking towards more flexible factories, where production machinery can be moved or updated, without the need for new fiber. They are gathering more data from sensors to improve productivity and preventative maintenance. This all points to faster and better wireless infrastructure.
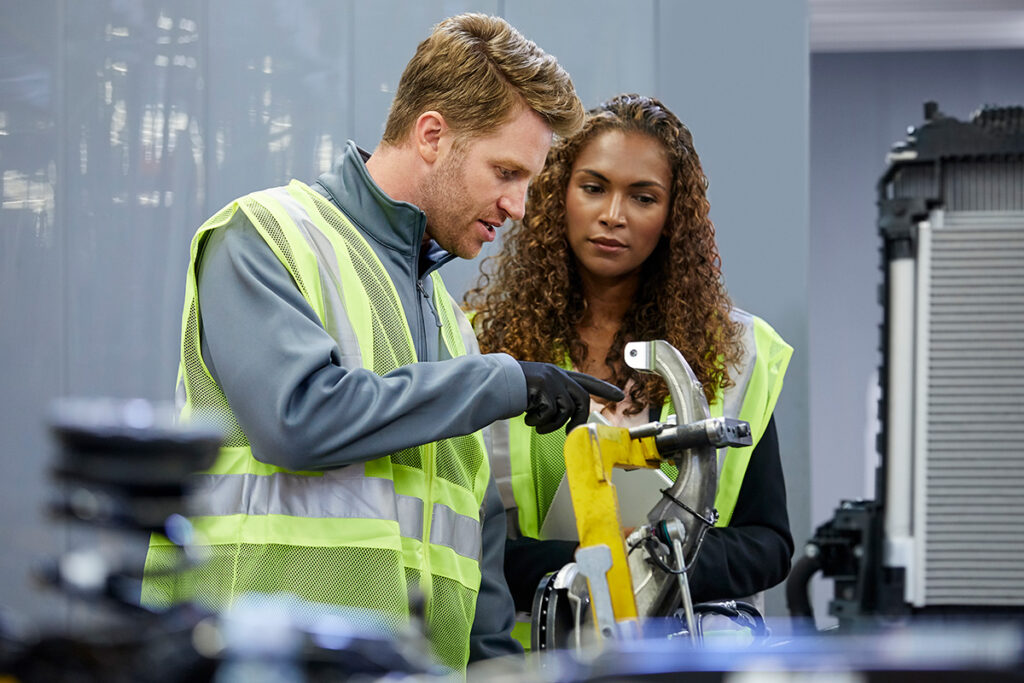
Process monitoring & supply-chain management
At a higher level than individual production systems, larger manufacturing companies want an overview of their entire operations, which can span multiple plants (perhaps internationally dispersed) and partners.
By collecting operational data “from the ground up” and collating it into dashboards spanning multiple sites and supply-chain elements, companies will be able to enhance just-in-time and other inventory-management and performance-optimization techniques.
Clearly, this will go beyond private 4G/5G connectivity – it requires enhanced data collection via all network means on premise, as well as wide-area links between different production facilities. There are already some CSPs and cloud providers attempting to enable these types of solutions.
There is already a tight integration of private cellular with various forms of cloud/edge computing. This will likely expand, with the wider use of IoT analytics, ERP (enterprise resource planning) systems and other platforms that ultimately exploit private networks, sensors and real-time data feeds.
Robotics
While some industries such as auto-manufacturing have long had wide use of robotic systems, many other subsectors have been far less automated.
Various trends are now occurring:
All of this is driving the need for more (and better) wireless connectivity for robotics. Again, 5G is seen as an important enabler in many cases.
In addition, 5G’s improving location/positioning capabilities enable proximity-sensing between humans and mobile robots to be more accurate. In future, we may also see “centaurs” – collaborations of robots and humans for specific tasks.
Machine vision quality inspection
There is a growing use of video in manufacturing processes. Cameras are used for production-line inspections, which can reduce wastage, improve final product quality and enhance yields.
A broad range of AI-enhanced approaches can analyze patterns, or detect flaws such as cracks, in ways which may not be possible by human workers. Machine-vision systems on-premise or in another edge-computing site can analyze images for misformed welds or infra-red signatures of other issues.
Techniques such as additive manufacture (3D-printing) or precision-welding need close monitoring of quality during the process. This enables mistakes to be corrected instantly – or part-finished products to be rejected without waste of further time or expensive materials. However, this needs huge amounts of data to be communicated and processed rapidly, as correcting problems may have to occur within milliseconds.
5G’s reliability, latency and throughput speeds are ideal for real-time streaming video feeds from high-definition cameras, especially in locations which are tricky to connect with fiber.
This is a core use-case for private 5G, especially as these functions tend to be indoors, and in areas needing customized network coverage because of machinery, concrete and other structural components of the building.
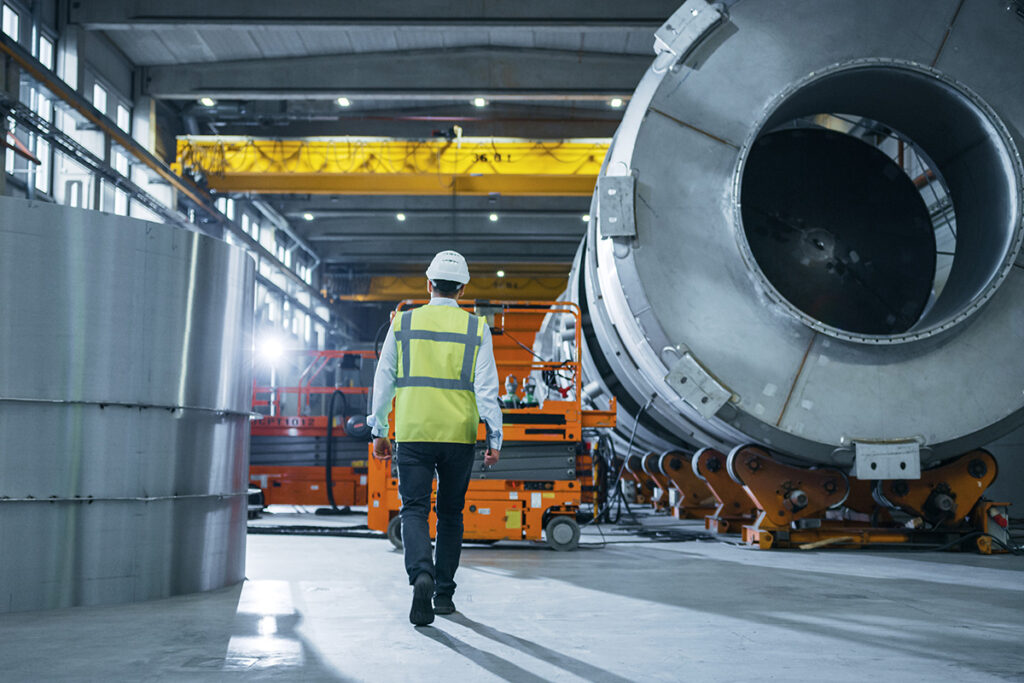
Precise asset location and positioning
There are numerous purposes for asset-location and real-time positioning in manufacturing environments. Robots and AGVs need to take material from specific locations on warehouse shelves or other stores, to particular machines or conveyor belts. They need to dock accurately with charging stations, accurately locate any faults, and ensure safe distances from humans and delicate machinery. Tools need to be tracked and located, as well as other assets such as trolleys which are frequently moved around.
This can improve manufacturing productivity and asset utilization, as well as reducing the risks of theft by “geo-fencing” within specified boundaries. Tracking technologies also contribute to preventative maintenance, by ensuring items are stored in correct locations.
It is already possible to use a variety of wireless technologies (including private deployments of 4G NB-IoT) for asset-tracking, but real-time positioning, especially indoors, is hard.
Later versions of 5G, especially 3GPP Release 17 onwards, will permit highly accurate location tracking, down to centimeter-scale positioning. On a well-engineered private network, this would have multiple use-cases in manufacturing.
Mobile control panels
In industrial settings, control panels (also called HMIs – Human-Machine Interfaces) are electronic displays that allow operators to monitor and control automation systems, from individual machines to entire production-lines. They often also support safety-stop buttons for instant intervention in dangerous situations.
In many cases, HMIs are physically wired into systems directly, but there is growing desire for untethered operation, with wireless connections making the devices seem like conventional ruggedized tablets.
While such panels can use Wi‑Fi, in some cases the reliability and low-latency capabilities of 5G may be advantageous – plus it also means they can be used by staff operating remotely or outdoors.
As with several of the use-cases discussed in this section, the safety-critical aspect of such control panels tends to make private 5G (where possible) more desirable than public networks.
Site-wide networks & workforce communications
At present, many manufacturing-industry deployments of private 4G/5G tend to be used just in specific buildings, or even for individual processes or machines. However, as with other sectors such as ports, over time some entire plants will be provided with site-wide (or “campus”) networks, perhaps covering both outdoor and indoor areas. Such networks could enable multiple applications and service functions, but at a broader level of coverage. For example, this could include:
For such purposes, coverage is needed over wide areas, with the largest manufacturing plants several kilometers in size, as well as inside warehouses, vehicles and factories. Cellular 4G/5G networks are more flexible than traditional site-wide VHF radios or PMR (private mobile radio) systems – and support data applications with far greater capacity. Wi‑Fi can be used for small plants, but is less viable for the larger facilities.
Smart sensors & digital twins
“Digital twins” are virtual partners of real machinery – or indeed entire plants. By instrumenting automation systems or other production assets with sensors, and by capturing data directly from the controllers, it is possible to create simulated versions of real-life equipment.
This “twins” can be used to tune performance and output, observe signs of imminent problems and perform preventative maintenance, or optimize aspects such as energy usage. By comparing data from multiple similar pieces of equipment, it may be possible to spot operator errors, or design flaws which could be fixed or retrofitted.
Such systems have a wide variety of connectivity requirements – and obviously this will depend on factors such as mobility. Counter-intuitively, some older legacy machinery might use external wireless-connected sensors (such as temperature / vibration monitors) while newer systems may have such capabilities wired-in.
Although there are many different wireless options for this type of use-case, 5G offers potential benefits in sensor capacity, reliability, and density of meters supported per base-station. It can also support high-bandwidth inputs such as video or LiDAR sensors.
Video surveillance systems
Manufacturing companies have significant needs for video surveillance, as well as video-based production systems and quality control. These monitor security and safety risks such as fire, intrusion and theft or other illegal activities, potentially over large site area, both indoors and outdoors.
For example, many manufacturing companies have large areas for storage of vehicles, or stockpiles of valuable materials. Some sectors such as aviation and shipbuilding have obvious security concerns, while some sectors face additional risks from geopolitical actors or espionage.
Wireless connectivity with 4G and 5G allows extra capacity for high-resolution imaging, as well as reduced latency. Increasingly, cameras are attached to mobile assets such as vehicles, robots and drones, which obviously necessitates wireless access. Over time, edge-computing with machine vision will enable additional automation.
Other use-cases
There are numerous other use-cases for private networks emerging. Some will be highly sector-specific. Some examples include:
Why deploy private networks?
The second question mentioned above is at the core of this report. Why are these use-cases better suited to private 4G/5G rather than public network services from MNOs?
Looking across industry overall, there are many company- and site-specific reasons that drive firms to look at private wireless solutions. However, broad patterns are visible.
There are five top-level rationales that Disruptive Analysis uses to discuss Private 5G:
The following sections describe these in greater detail.
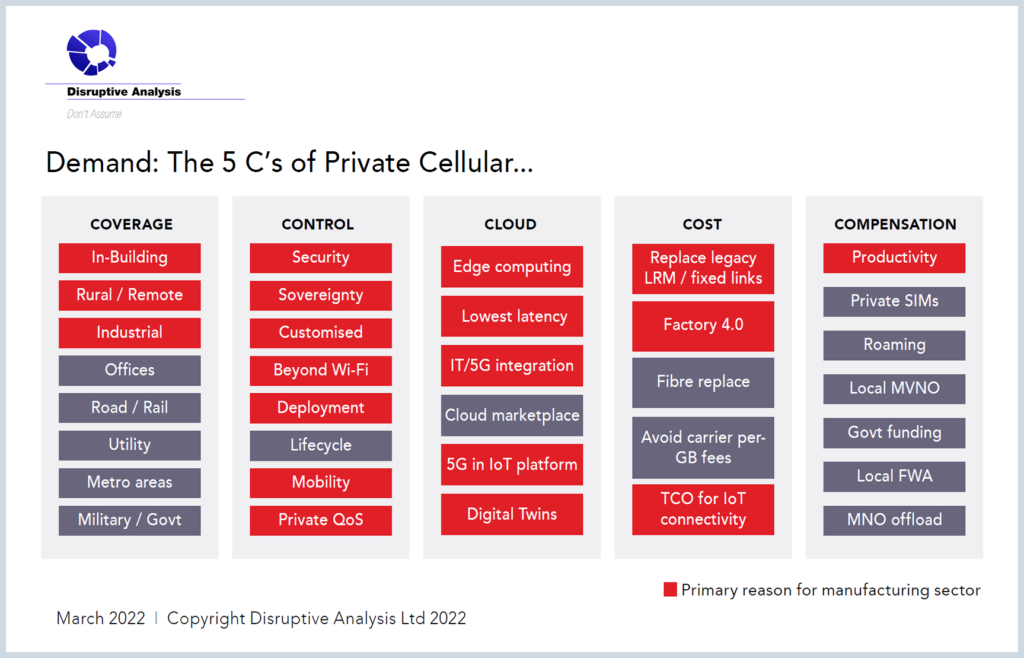
Coverage
A core reason for using private 4G/5G, rather than public MNO services, is the limitations of network coverage. MNOs tend to deploy network assets in areas with high population density, or along main roads.
Manufacturing companies’ facilities often have relatively poor coverage, as industrial zones tend to be located away from major population centers and residential / business districts.
In addition, in-building coverage is especially poor for factories, given the common use of metal and concrete in construction, fewer windows compared to other sites, and various forms of screening and pipework.
Control
This is the most important aspect of private networks for manufacturing companies. Many firms, especially large or high-tech companies in sectors like automotive and electronics, have extremely high costs of any down-time, as well as being very protective of data assets.
Owning and operating 4G/5G wireless systems allows firms to define and optimize many network parameters themselves, taking direct responsibility for security, reliability, performance and reporting. They can also integrate them directly with other IT / OT and network systems, especially where there are legacy protocols involved, where telcos lack knowledge and experience.
They can choose their own mechanisms for redundancy and cybersecurity, aligning with sector-specific best practices and regulations. For demanding applications like streaming video or low-latency grid control, they can customize and optimize radio resource management and redundancy.
In the longer term it may be possible for enterprises to obtain a “slice” of public MNO 5G networks and obtain better control and service-level agreements, but this remains an unproven model and is dependent on future versions of the 5G technology. Similarly, the appeal of linking private and public networks via “roaming” is debatable – robots don’t leave the factory grounds, while trucks and workers’ smartphones can likely support multiple SIMs.
Cost (and risk-avoidance)
Many manufacturing companies have traditionally had only limited use of public 4G/5G networks for on-site use. While they have used normal cellular contracts for their staff smartphones and fleets, there is relatively little scope for switching public for private networks for in-factory automation or other similar use.
Instead, the potential cost savings from private cellular are more related to displacement of fiber runs, especially for machinery that may be moved around, or for remote connections such as perimeter security cameras.
While the general Industry 4.0 models should also improve manufacturers’ economics, relatively few aspects are purely driven by private cellular – most can also be enabled with Wi‑Fi or other connections, albeit perhaps with less reliability in some circumstances.
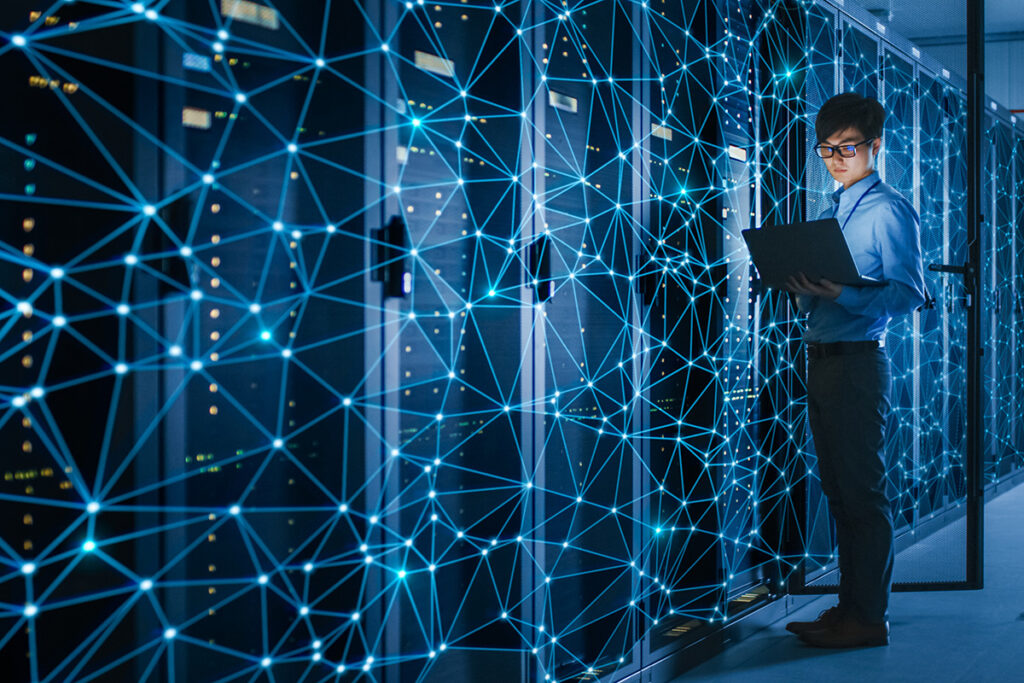
Cloud
Across the manufacturing sector, there is a growing link between private wireless and cloud platforms, and especially the use of on-premise or near-premise edge computing.
There are two linked trends here:
In recent months, many of the largest cloud companies have announced initiatives around private 4G/5G, either directly selling to enterprises, or working with systems integrators and MNOs to deliver hybrid solutions.
Compensation / Monetization
Unlike some sectors such as airports or property companies, there is limited scope for manufacturing companies to directly monetize private 4G/5G, for instance by offering connectivity services to tenants, or neutral-host functions to public MNOs.
Certain very large manufacturers – for example the suppliers of industrial automation equipment, or construction/mining systems – could embed private cellular directly into the solutions they sell to their manufacturing customers, or act as “industrial mobile operators” in markets with available spectrum.
Spectrum options and trends
Overview
A key ingredient for manufacturing-sector private networks is access to suitable spectrum for 4G/5G. This domain involves a huge range of trade-offs in terms of coverage, capacity, cost, device availability – and also politics and regulation.
It also directly relates to the relevance and potential for “pure” private networks run by enterprises or specialists, versus those that are provided as a managed service by a mainstream telco that primarily runs public 4G/5G networks.
Historically most spectrum suitable for cellular networks has been awarded on an exclusive regional/national basis to public mobile operators (MNOs), often through auctions.
Manufacturers have historically had little direct access to such mainstream bands without rare and complex leasing arrangements, while other frequency ranges had few radios or devices available. But this is now changing rapidly, as various national regulators make local licenses or various forms of shared spectrum available – and device / chip companies start to support them as well.
At the same time, MNOs are becoming more open to a range of new engagement models, including the creation of private campus networks which are not linked to their main macro infrastructure – in essence, acting as systems integrators for custom projects.
For private networks there are, broadly, three spectrum options:
The following sections give more detail on some of the specific bands being made available around the world.
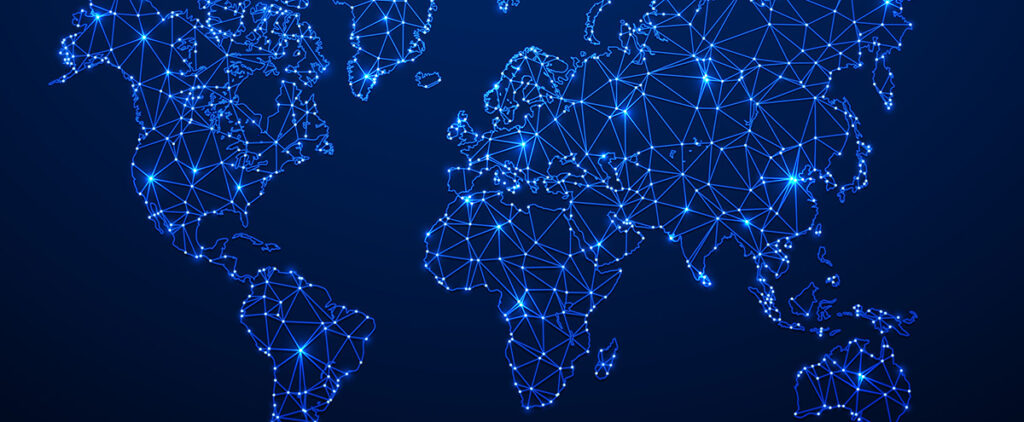
CBRS and other mid-band options
For site-specific or regional coverage, a growing number of countries are making sections of mid-band spectrum available for manufacturing companies (as well as other enterprises). Typically this is based on some form of spectrum-sharing, with either manual or database-driven licensing for specific areas and band rights. Industry 4.0 advocates have been some of the most powerful voices persuading governments and regulators of the potential economic benefits.
Among the most important examples are:
A number of other countries in Europe and the EU regulatory advisory body RSPG have also suggested the 3.8-4.2GHz band for future potential shared/enterprise use. Many other countries have ongoing regulatory initiatives or consultations on suitable mid-band options for industry, including Spain, India and Saudi Arabia.
Other markets have the potential for local leasing of MNOs’ allocated national spectrum (for instance in Australia, Sweden and Denmark), or the ability for regional operators specialising in industrial networks to obtain ordinary licenses in sparsely-populated areas (for instance in parts of Canada).
The main exception is probably China, which still tends to favor MNO national licensing.
It is also worth noting the potential for using unlicensed bands at 2.4GHz, 5GHz and increasingly 6GHz as well for private 4G/5G – although the lack of interference protection may limit the scope for mission-critical applications.
Sub-1GHz options
Low-band spectrum has only limited relevance for manufacturing, as it is mostly suitable for wide-area communications such as utility companies’ push-to-talk networks. However, it may be suitable for very large manufacturing plants, or multi-site facilities distributed over a wide regional area. Its good indoor / underground propagation may also be useful for IoT in some cases.
A number of markets have made such bands available to.
It is also possible to use narrowband IoT versions of 4G (NB-IoT & LTE Cat-M) in the various sub-GHz allocations, either licensed or unlicensed.
mmWave
A number of countries, including Germany, UK, Finland, Malaysia and Japan, have made 26GHz, 28GHz or other high-band spectrum available for local use. In the US, Italy and South Korea, some MNOs are also examining opportunities around mmWave private networks. This is mostly targeted at indoor/campus sites such as factories, warehouses and mines. Key use-cases are for local high-capacity usage, such as remote-driven vehicles or high definition cameras, especially where mounted on vehicles or robots.
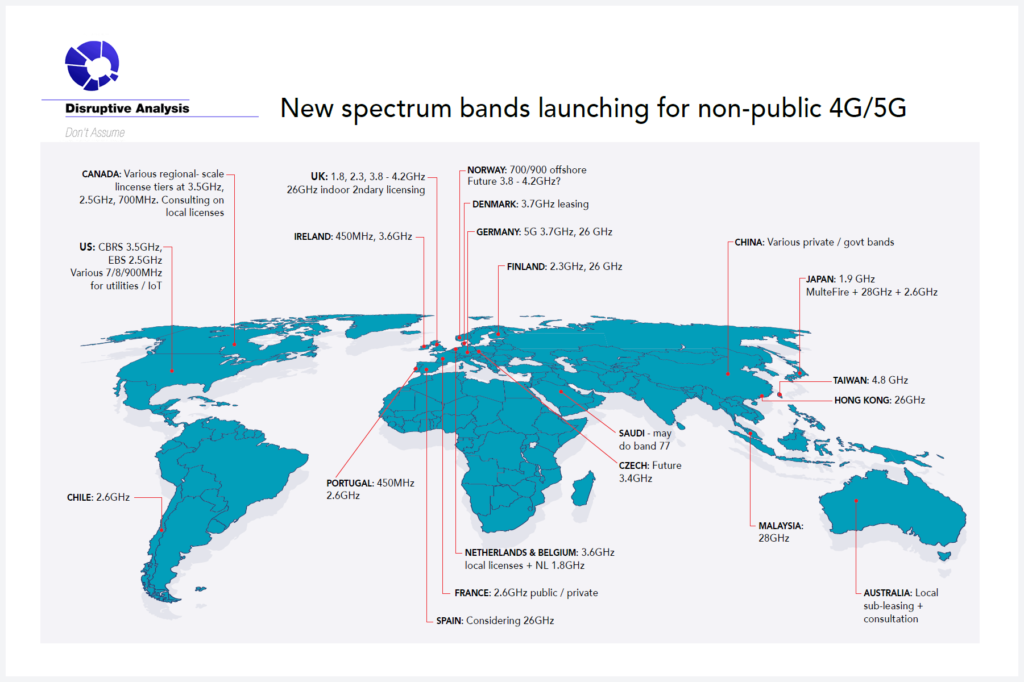
Copyright Disruptive Analysis Ltd 2022
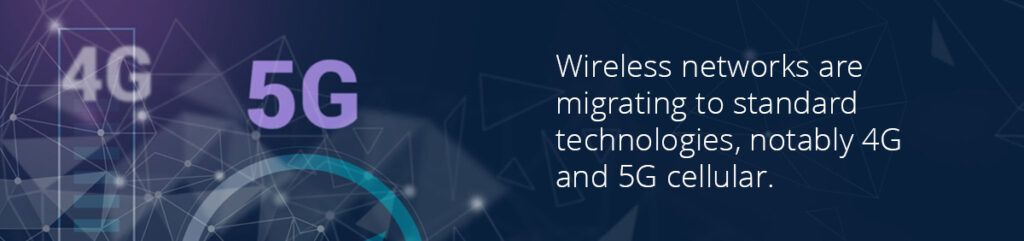
Conclusion & long-term futures
The manufacturing sector is likely to be one of the leaders of the mainstream adoption of private cellular networks. It takes private 4G/5G beyond the early adopter sectors requiring “critical communications” and more into the realm of IoT / OT (Operational Technology) connectivity, as well as more conventional IT-type applications comparable to Wi‑Fi use today.
While this report has focused on the radio aspects of private 4G/5G, it is important to recognise that the broader ecosystem – from core networks to edge computing and planning / design / test systems – is evolving in tandem, along with a huge range of systems integrators and vertical specialists. In manufacturing organisations like the 5G-ACIA (Alliance for Connected Industries and Automation) are defining best practices and standardised terminology.
The growing maturity of enterprise-grade 5G technology, plus the wider availability of local or dedicated spectrum for enterprise use suggests a continued healthy dynamism for many years to come. By 2025 there may be 1000s of private networks in manufacturing, and perhaps tens of 1000s.
Yet despite similarities across sub-sectors and countries, what seems likely is that the specific use-cases and deployment scenarios will vary considerably. Some markets are primarily releasing mid- and low-band spectrum for enterprises, while others are more focused on mmWave or new unlicensed options.
That said, it should be noted that many larger manufacturers will be cautious and gradual, introducing private cellular through a progressive phasing of trials and mid-size field deployments. Many of the current sites use private cellular just for specific buildings, or even individual machines or applications.
In addition, while greenfield manufacturing sites may be “5G primary”, in most instances there will be significant installations of other network technologies in place. This spans from various versions of fixed ethernet and Wi‑Fi, to a broad array of dedicated industrial systems. There will also be many incumbent suppliers such as industrial automation companies, that will often act as channels or integrators for (often own-branded) connectivity systems. The 5G industry needs to fit into, or around, these incumbents.
Table: Examples of Manufacturing company private 4G/5G deployments/trials
Company | Country | Sector/Purpose | Spectrum/Owner |
---|---|---|---|
John Deere | US | Tractors & construction equipment | CBRS PAL for 4G/5G |
Worcester Bosch | UK | Consumer electricals (sensors & robotics) | Trials at 2.6GHz / 3.4GHz |
Ford | UK | Automotive (trial of new welding etc.) | Vodafone licensed band |
Ford | US | Automotive (multiple use-case at EV plant) | AT&T spectrum |
Inventec | Taiwan | IT Hardware (optical inspection, AGVs) | Likely 4.8GHz local 5G |
Volkswagen | Germany | Automotive (smart factory trials) | 3.7-3.8GHz local license |
Haier | China | Consumer electricals (optical inspection) | Unclear – China Mobile |
Nokia | Poland | Telecoms eqpt (AGVs, sensors, comms) | Orange Poland spectrum |
Butachimie | France | Chemicals (asset-tracking & comms, 4G) | 2.6GHz |
Foxconn | US | Electronics (AGVs, robotics etc.) | CBRS |
BMW | Germany | Automotive (multiple plants & applications) | Likely 3.4-3.8GHz |
Konecranes | Finland | Cranes (trial for ports, eg mobile cameras) | Unclear. Likely 3.4GHz |
AS Plastik | Croatia | Vehicle components (factory automation) | Unclear |
ArcelorMittal | France | Steel (multiple sites / use cases) | Unclear likely 2.6 + 3.4Ghz |